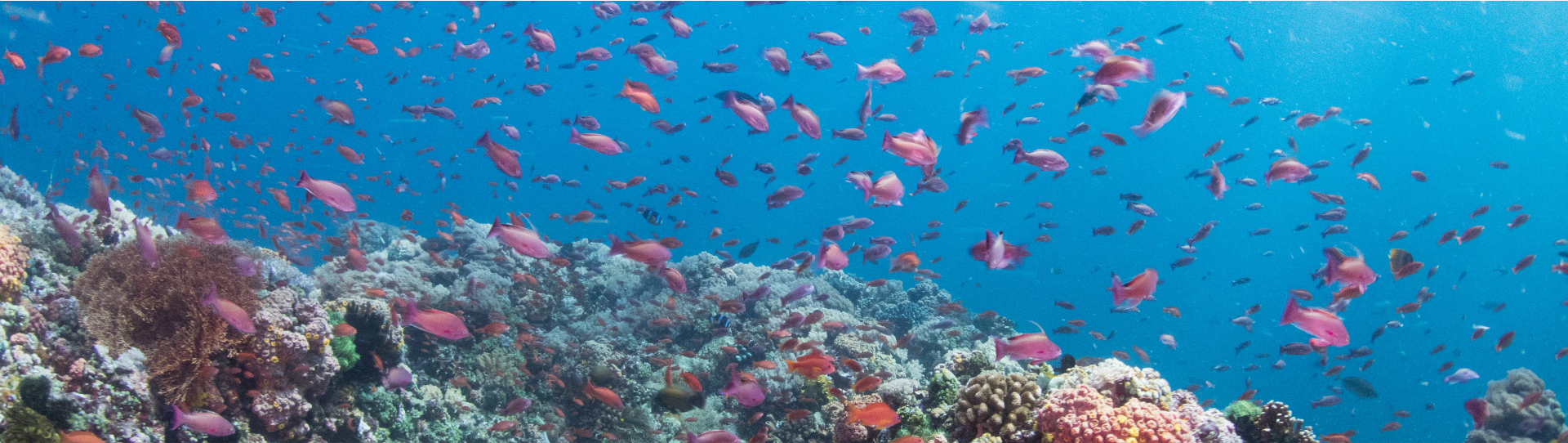
Designing the perfect core structure
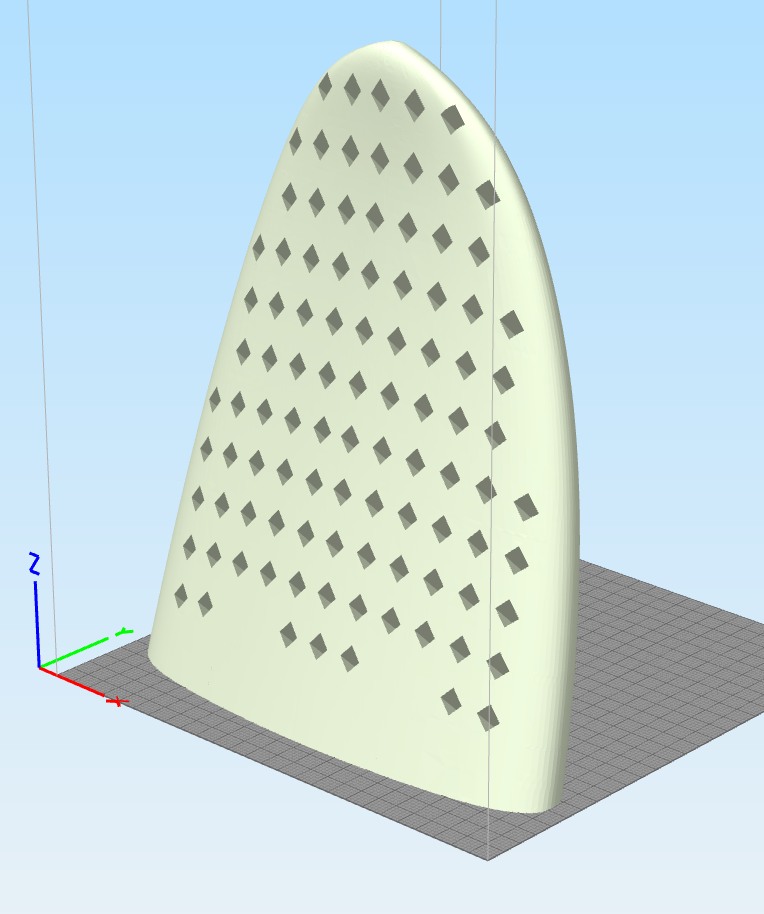
Lattice strucures
Lattice structures 3D printed in PETG offer a strong yet lightweight solution for various applications. By incorporating holes in the vertical sections, material usage is optimized, reducing weight without compromising structural integrity. PETG's durability and flexibility make it ideal for these designs, ensuring resistance to impact and environmental factors. This approach is particularly useful in aerospace, automotive, and custom engineering projects where weight savings are crucial.
It is also being explored in windsurfing boards with monocoque structures, where 3D-printed lattice cores are combined with bioepoxy and flax fiber reinforcements. This results in a high-performance, eco-friendly construction that enhances strength, flexibility, and responsiveness while keeping the board lightweight.
Core experiments
Designing the perfect windsurf board core requires a balance between strength, weight, and performance. Using Fusion 360, engineers can create CAD-based designs to analyze structural integrity before production. By incorporating 3D printing and rapid prototyping, different lattice structures can be tested efficiently to optimize weight distribution and durability.
A honeycomb deck is integrated into the core, enhancing stiffness without excessive weight. Various lattice geometries, such as gyroid, hexagonal, or voronoi patterns, are evaluated for impact resistance and flex characteristics. Computational simulations in Fusion 360 help determine the best combination for maximum performance in high-wind conditions.
With iterative prototyping, designers can refine the board's buoyancy, flex, and durability, ensuring an ultra-light yet strong windsurf board that pushes the limits of speed and maneuverability.
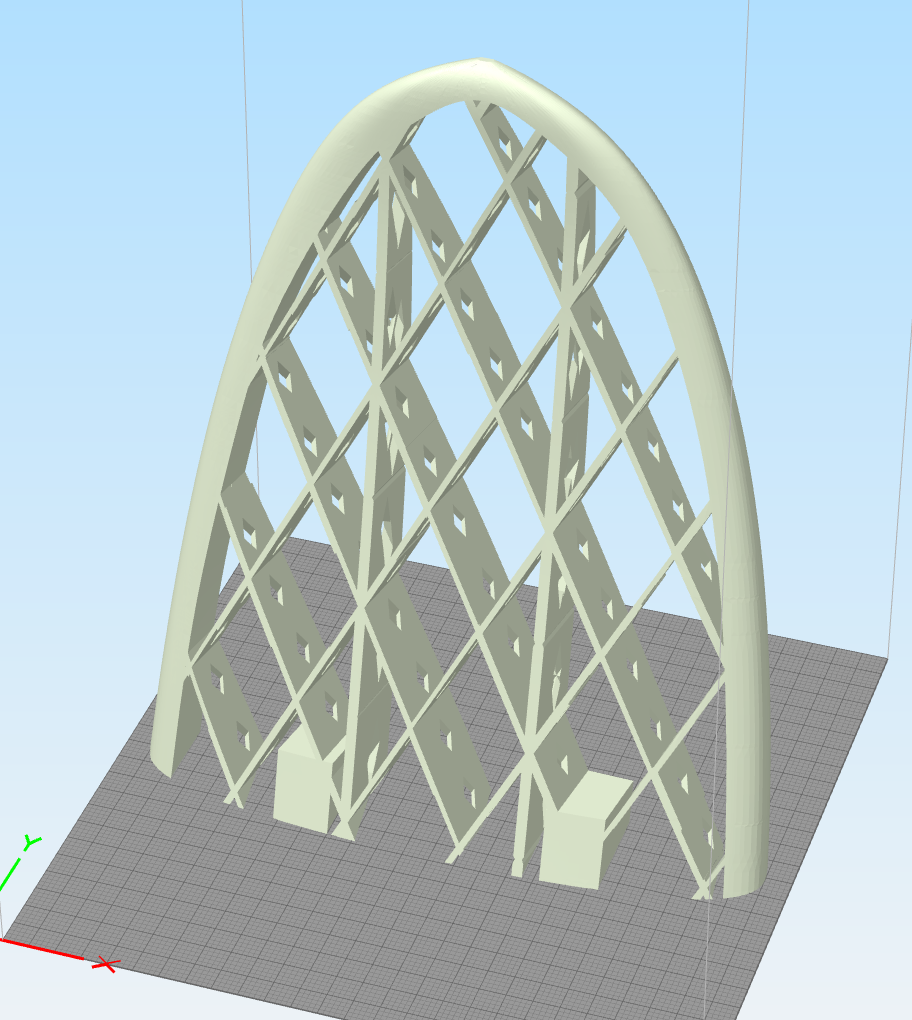