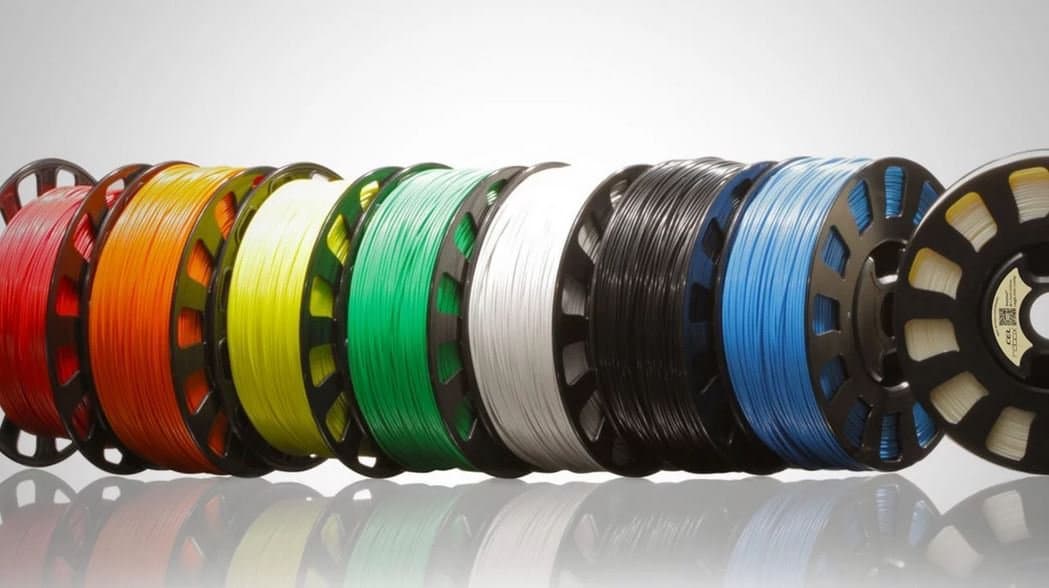
Experimenting with filaments and 3d printed cores
Exploring Sustainable 3D Printing: Recycled Filaments in Action
The soul surfer project investigates the potential of eco-friendly 3D printing by experimenting with unconventional recycled filaments. We're testing materials like up-cycled fishing nets to evaluate strength and flexibility, alongside recycled polypropylene for its lightweight properties. The goal is to assess printability, mechanical performance, and sustainability, pushing the boundaries of responsible manufacturing.
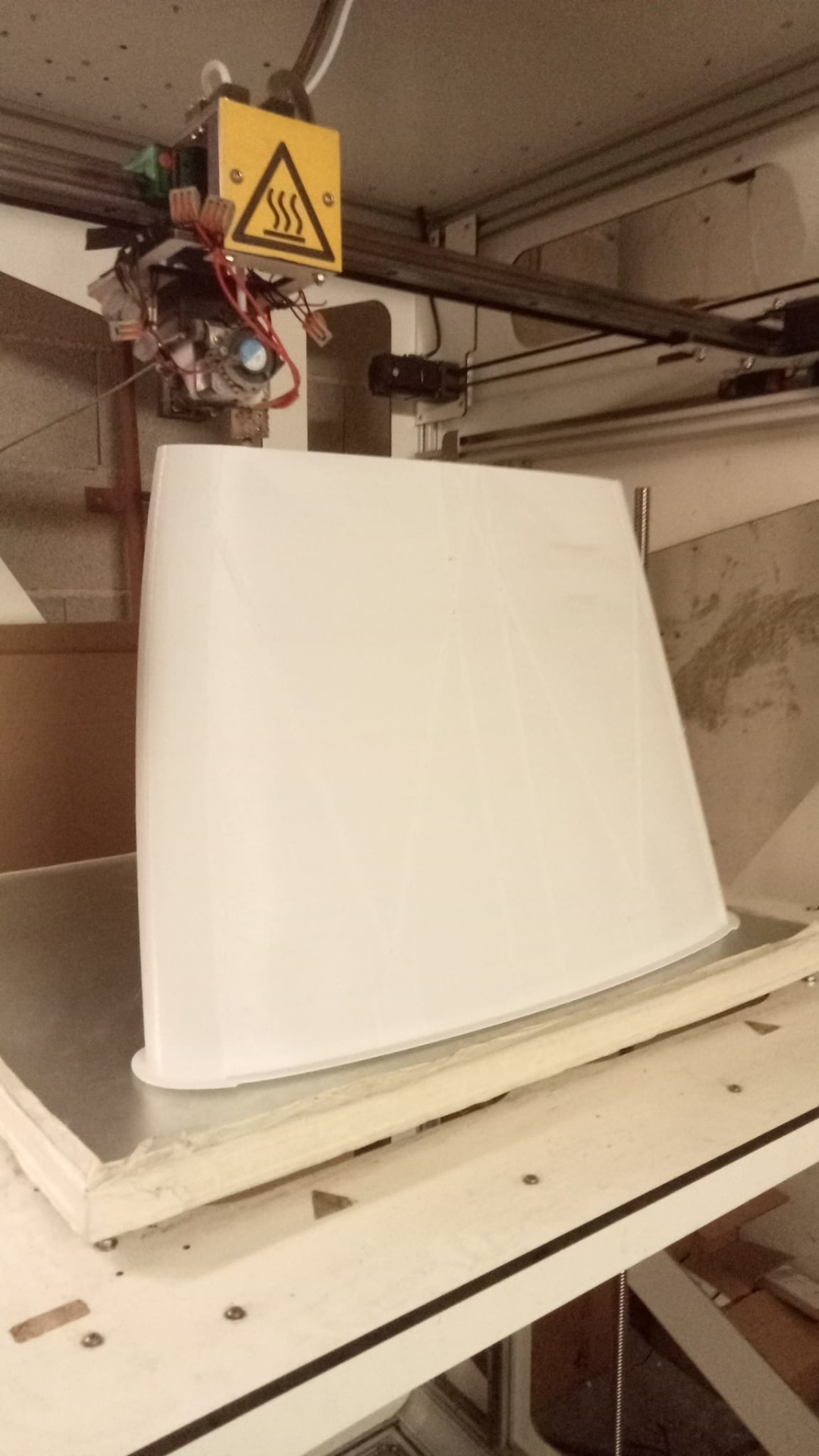
Fine-Tuning Printer Parameters
Dialing in the perfect print settings is a process of iteration. Some key parameters to optimize include:
Print speed: Slower speeds improve accuracy and adhesion, reducing defects.
Layer height: A balance between print resolution and speed; 0.2-0.3mm is often a good compromise for structural parts.
Infill density: A honeycomb or gyroid infill pattern helps to maintain strength while minimizing weight.
Extrusion rate: Adjusting for consistent flow to prevent under-extrusion or excessive material buildup.
Bed adhesion aids: Using a PEI sheet, glue stick, or specialized adhesion promoters can further enhance first-layer bonding.
Achieving a Lightweight Core
The final goal is to create a strong yet lightweight nose structure. By strategically tuning infill density and using reinforced perimeters, it is possible to achieve a high strength-to-weight ratio. A lower-density infill combined with solid outer walls ensures impact resistance while keeping overall weight manageable. Additionally, post-processing techniques such as sanding and epoxy sealing can further reinforce the printed component and improve its hydrodynamic properties.
3d printing @ Yuyo Montpelier
3D printing the nose of a windsurf board using recycled PETG presents a unique set of challenges, primarily related to warping and layer adhesion. Achieving a strong, lightweight core requires meticulous fine-tuning of printer parameters to optimize print quality and mechanical strength.
Overcoming Warping Issues
Warping is a significant issue when working with PETG, especially recycled material, due to its tendency to contract unevenly as it cools. To mitigate this, a heated print bed is essential, ideally maintained at temperatures between 70-90°C. Enclosing the printer or using an actively heated chamber helps to maintain consistent temperature distribution and reduce thermal stresses that cause warping. Additionally, printing with a raft or brim improves bed adhesion and minimizes distortions at the edges.
Enhancing Layer Adhesion
Strong layer bonding is crucial for the structural integrity of the board nose, as it must withstand impacts and hydrodynamic forces. To enhance interlayer adhesion, adjusting the extrusion temperature is key. PETG generally prints well between 230-260°C, but for recycled variants, slight adjustments may be necessary depending on the specific material properties. Slower print speeds (around 30-50mm/s) and higher extrusion multipliers help ensure layers fuse properly, preventing delamination. Cooling should be carefully managed—too much cooling can cause weak bonds, while too little can lead to excessive stringing and oozing.
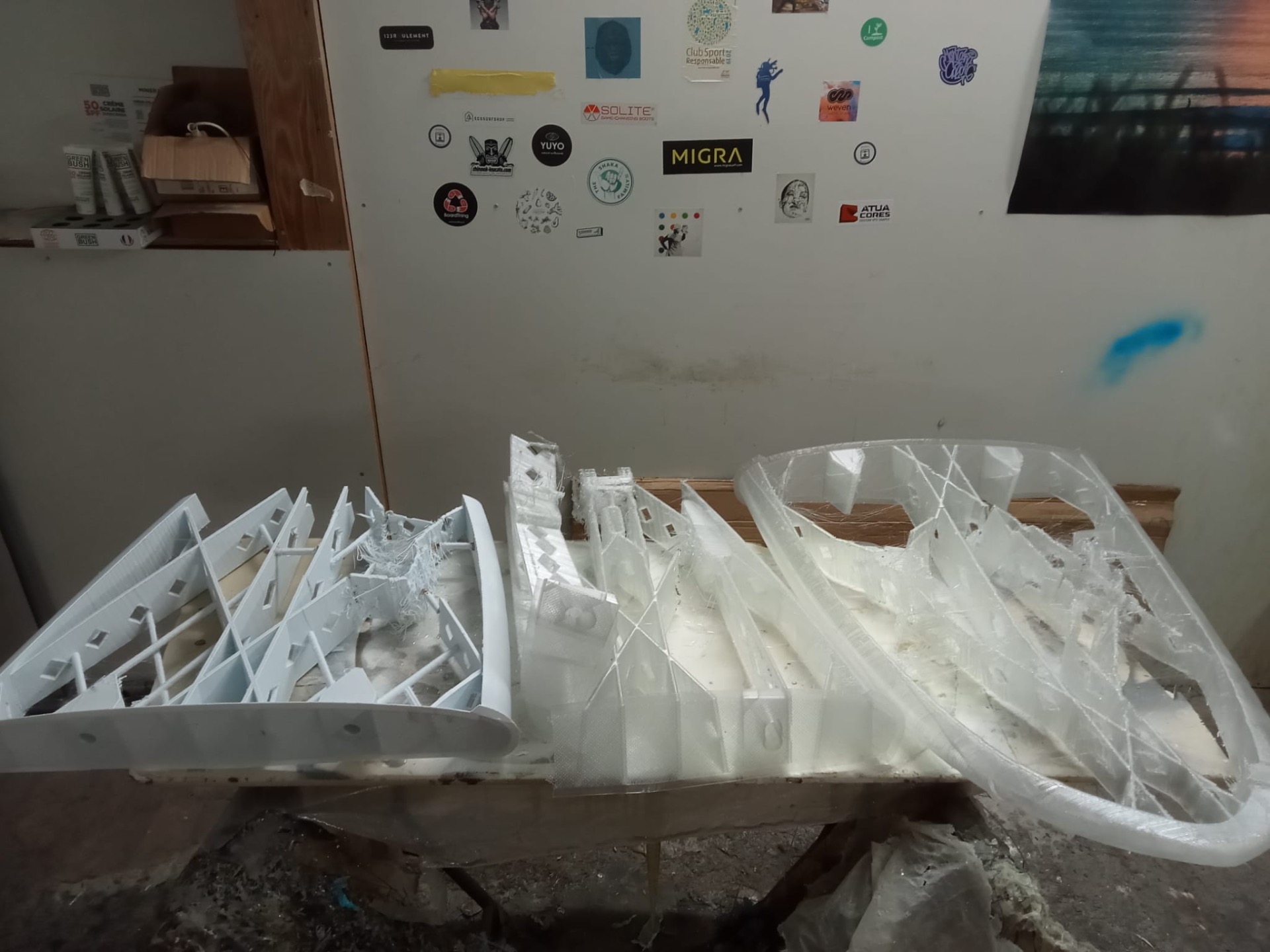
By addressing these challenges through precise printer calibration and careful material handling, 3D printing a windsurf board nose with recycled PETG becomes a viable and sustainable approach to board repair and customization. This technique not only reduces waste but also opens the door to innovative, performance-oriented board modifications.